A team of designers in Jerusalem intends to swap emission heavy materials like concrete and reinforced steel for 3D printed living structures made entirely of natural resources.
3D printing has come a long way in the last 20 years and is slated to become $56bn market by 2027. In the last year alone, we’ve written about sustainably printed fashion, design homeware made from food waste, and even printed vegan steaks.
The latest obscure use of the tech involves printing layers of upright, living 3D soil. As part of Jerusalem’s Design Week, an installation called ‘To Grow A Building’ was unveiled and featured a dozen dirt structures – all of which contained dense green roots and even edible radishes.
Reminiscent of a concrete pump, a custom designed machine had been fed with seeded soil and used to form several geometric shapes of different sizes. From there, fertilisers and regular watering ensured that natural plantation would bloom and reinforce each structure.
This may sound experimental, but it’s far from just a display of technology. The installation is rooted in very pragmatic and pertinent concerns; chiefly, that the continual use of concrete and steel in the construction industry is responsible for around 22% of all global emissions.
‘We wanted to create architecture that is made out of totally organic and local materials that you don’t need to transport materials from the other side of the world,’ says Nof Nathansohn, an architect who worked on this project with a group of seven other designers.
If you’ve been following Thred for a while, you’ll likely know that this isn’t the first time sustainable materials have been printed in layers to create liveable structures. Nevertheless, it is definitely the first to offer pickable vegetables.
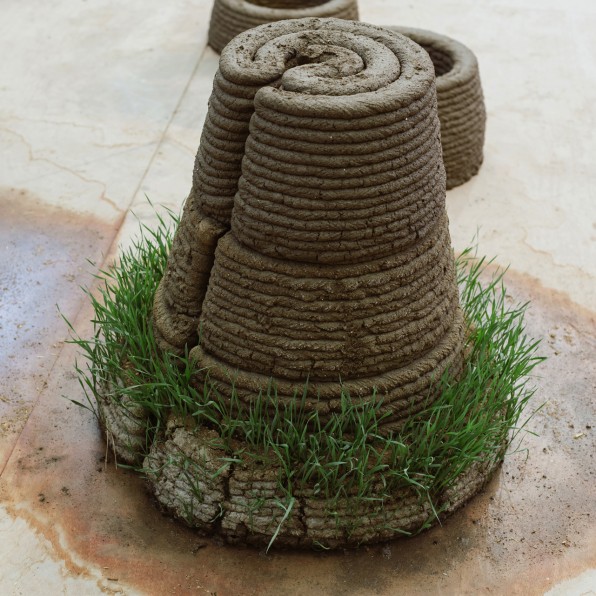