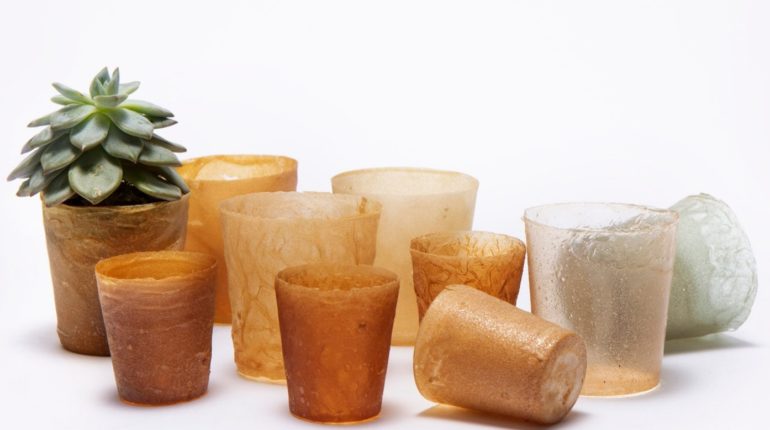
Shellworks – made from discarded exoskeletons of sea creatures
Shellfish, like fungi, have a secret: they contain the world’s second-most abundant biopolymer. This substance is called chitin.
The problem is that chitin must be chemically extracted from its source before transforming into a material that is ready to work with. So scientists created a commercial version of chitin called chitosan.
It may sound great, but the main drawback is that it is an expensive and time-consuming polymer to produce.
Looking to eliminate man-made chemicals and find an eco-friendly solution problem, four students at the Royal College of Art and Imperial College realised they’d need to invent an entirely new mechanism to extract organic chitin from shellfish.
Ed Jones, Insiya Jafferjee, Amir Afshar and Andrew Edwards put their heads together. After much deliberation, the end result was a set of five novel machines that work together to extract chitin and turn it into a biodegradable and recyclable bioplastic.
Each machine plays a key role, but things really come together after chitin is mixed with vinegar. This combination results in a material resembling paper, which can then act as a sustainable alternative to single-use plastic.
After gluing the newly made sheets together, the students have produced a line of cups made entirely from the biodegradable material. They’ve named it Shellworks.
Considering that the ratios of the mixtures can be experimented with to alter durability, colour, and transparency, the students hope the use of shellfish-based bioplastic will become widely used by major companies in the future.
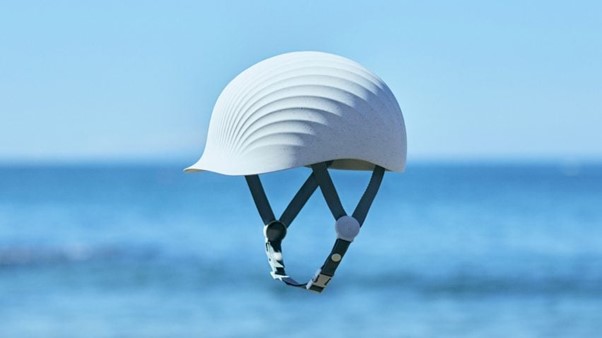
Shellmet – a hardhat made from seashells and recycled plastic
Ever wonder what happens to the shells you leave behind on your seafood platter? The truth is, most of them end up in landfill for many decades.
According to reports by the Japan-based TBWA/Hakuhodo agency, Japanese restaurants throw away 40,000 tons of scallop shells every year. This is a shame because their makeup is extremely strong and versatile.
In partnership with the Koshui Chemical Industry Co., the creative agency decided to make use of the waste coming from Japan’s favourite shellfish. After crushing them up, they are blended with recycled plastic to create protective hats for fishermen.
Designed to look like the ridged seashell it’s made of, the hard hat comes complete with a nylon strap for added security.
Its creators highlight how incorporating shells into this kind of design is special, because a protective shell that once protected scallops are getting a second run at protecting humans.
The hats are expected to roll out in Spring 2023 and come in pink, blue, cream, white, or black. The upside? They can be later recycled into new helmets or smashed up to create building materials.
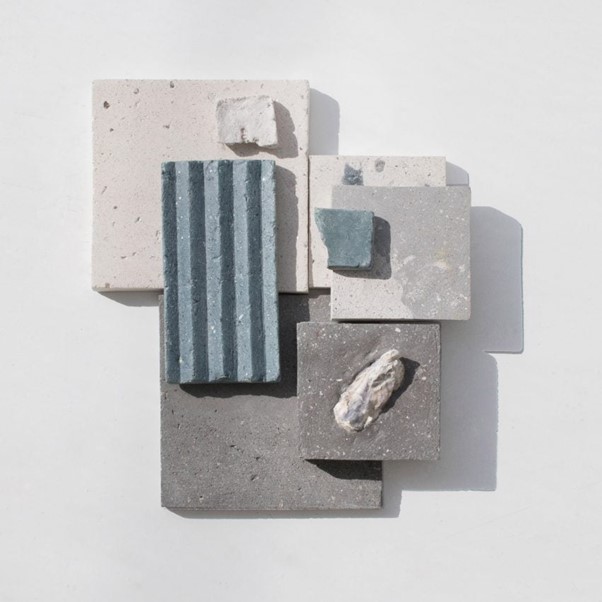
Sea Stone by Newtab-22 – cement blocks made from oyster shells
Like the inventors of Shellmet in Japan, the creators of Sea Stone were tired of seeing (and smelling) seashells from seafood and aquaculture industries piling up on their shores and landfills.
In efforts to give these materials another life, the team at Newtab-22 agency began grinding down oyster shells and combining them with organic, non-toxic binders to create a usable material. This material is something resembling concrete.
Seashells are no joke – they were once the sturdy homes of living beings after all – and are rich in calcium carbonate, aka limestone, which can be used to make cement.
As someone who grew up in a limestone house in Bermuda, I can verify that having this component makes seashells resilient enough to use in concrete. It’s so strong that it prevents housing damage when extreme weather and hurricanes visit the island.
In the first stages of Newtab-22’s trials, sugar and agar were trialled as organic binders for the ‘concrete’. Now, it reports using two custom-made binders that are currently pending patents.
Once this mixture is achieved, it is added to a mould and left to solidify into concrete-like pieces such as decorative tiles, tabletops, and vases. Employees at Sea Stone’s workshops are carrying out this mixing, dyeing, and pouring process manually, which makes each Sea Stone product unique.
Manual labour was chosen over machinery as it minimises the use of heat, electricity and chemical treatments, ensuring that production processes are sustainable and affordable.
Yet again, we’ve seen how nature has the answers to some of our hardest-to-solve sustainable solutions – so as long as we’re willing to do a little extra digging.